Overview:
This study explored how different levels of automation (semi-automated vs. fully automated) influence task performance, mental workload, and trust in automation in a collaborative manufacturing context. The goal was to determine the ideal balance between human control and robotic assistance in future hybrid workspaces.
Context:
Inspired by an observation at Setex Inc., an OEM car seat manufacturer for Honda and Acura located in St. Mary’s, Ohio. A worker reported pain from repetitive tasks. This observation bundled with the distinct separation between manual and automated operations was the primary motivation for this exploratory study combining experimental design and mixed methods research. This research sought to evaluate how collaborative robots (cobots) could alleviate physical strain while maintaining trust and efficiency.
The study was situated within the framework of Industry 5.0, which emphasizes human-machine collaboration over full automation.

Problem:
While robots excel at speed and precision, fully automated systems often reduce human oversight and can increase cognitive disengagement. On the other hand, too much manual intervention lowers efficiency.
How can we optimize cobot workflows to enhance performance without compromising human trust or cognitive engagement?
A hybrid workspace leverages a robot’s repeatability, precision, and speed alongside a human’s complexity, empathy, and flexibility. This approach, known as Human-Robot Collaboration (HRC), aims to create a shared environment where humans and robots work together. It bridges the gap between manual and fully automated production, involving human workers in direct interaction with machines, unlike fully automated setups where robots are typically separated from humans during operation.
Solution:
We designed a controlled experiment simulating a light manufacturing task involving human-robot collaboration.
Participants were assigned to two automation conditions:
- Automated Mode: The Robot acted autonomously without human intervention.
- Semi-Automated Mode: Participants controlled when the robot performed its actions.
Process:
Experiment Design:
Primary Task: Collaborative assembly of a miniature lamppost.
Secondary Task: Press a buzzer in response to randomized auditory stimuli (DRT).
Two Automation Levels:
Automated: Robot works without input after each step.
Semi-Automated: Robot waits for participant’s signal.
Metrics Collected:
– Task Performance: Assembly completion time
– Cognitive Load:
- NASA-TLX questionnaire
- Heart Rate (HR), Heart Rate Variability (HRV), LF/HF ratio
- Detection Response Time (DRT)
– Trust: Trust in Automation (TiA) scale
Participants:
58 individuals affiliated with LSU (students, faculty, instructors). All had normal or corrected vision and motor function. The majority had no prior experience with collaborative robots.
Task:
In this study, a participant was positioned near a collaborative robot and was tasked with assembling a miniature lamppost using magnetic wooden blocks, dowels, and a post-cap.
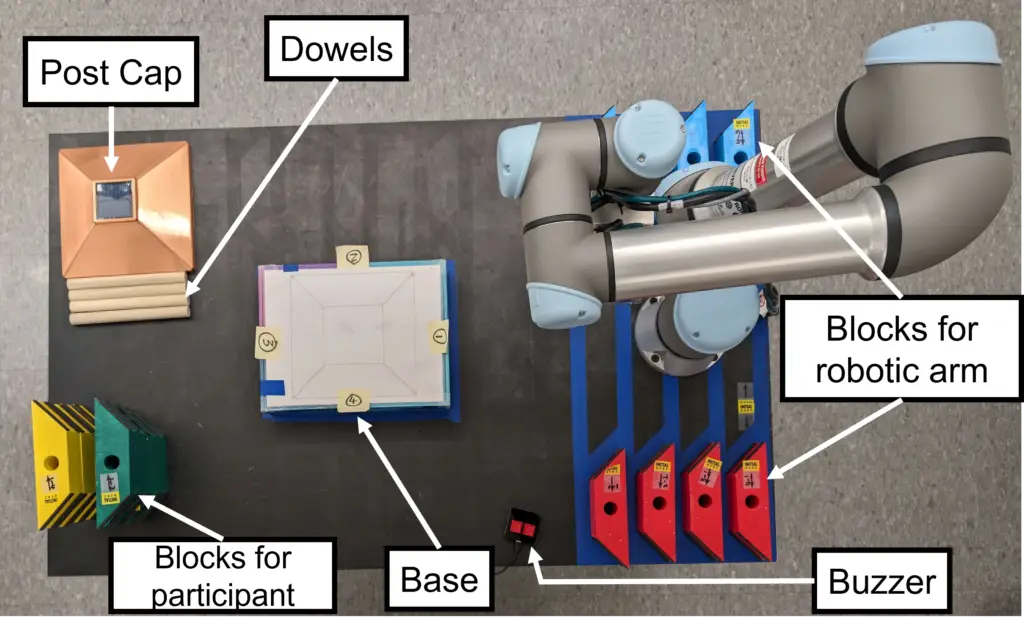
The participant and robot placed the blocks on the elevated base in a sequential order. Participants were divided into two groups:
- Automated Group: The participant shares control over the robot, which does not require activation after the participant’s turn.
- Semi-Automated Group: The participant has full control over the robot, which needs to be activated after each turn. (Video Link)
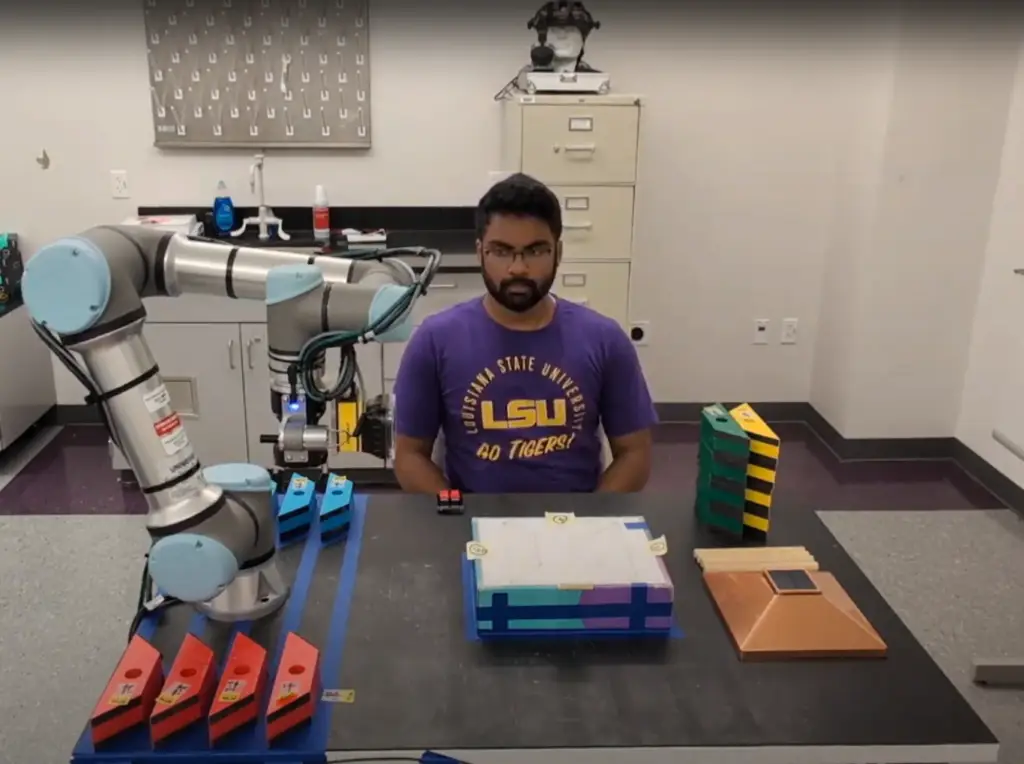
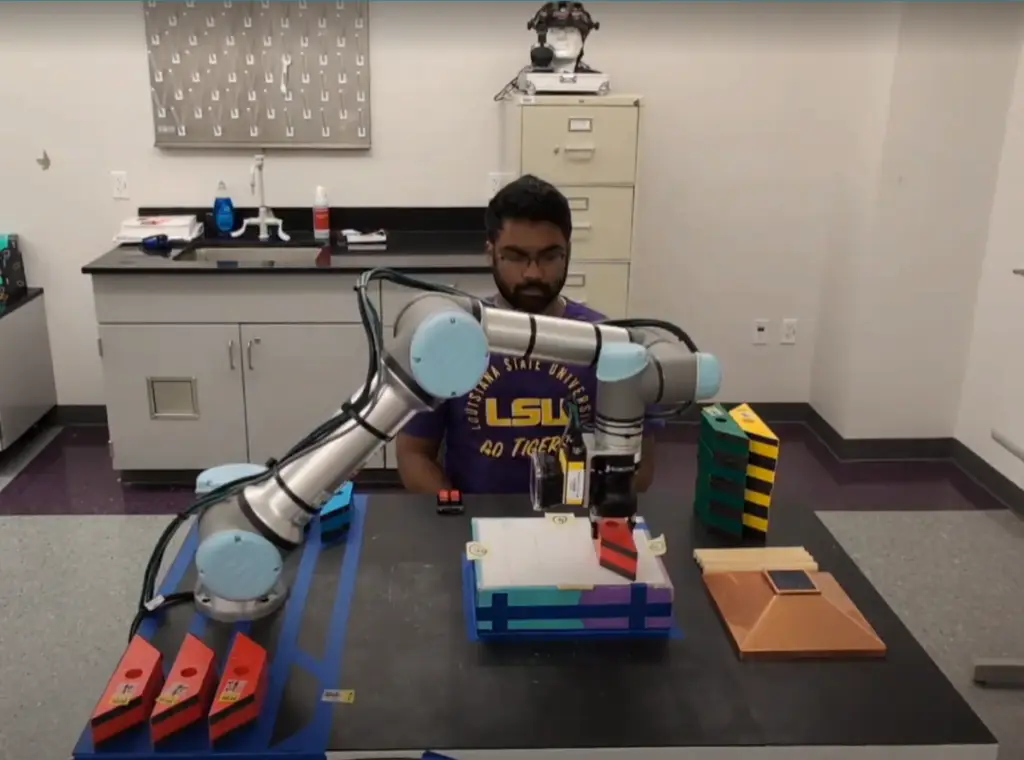
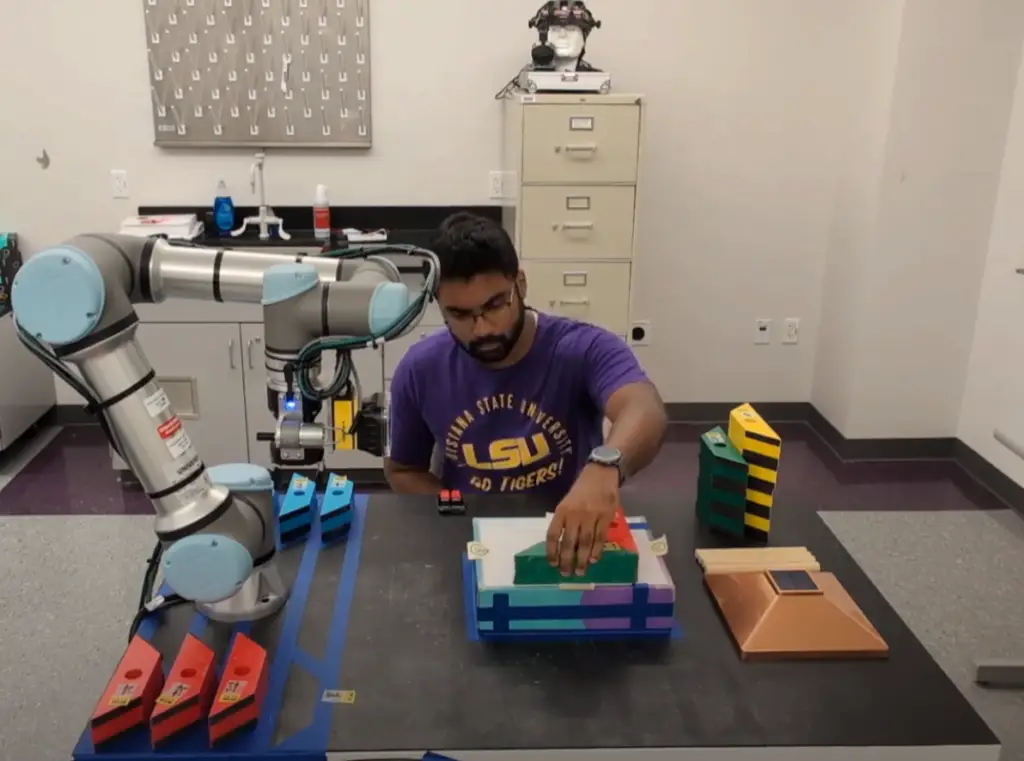
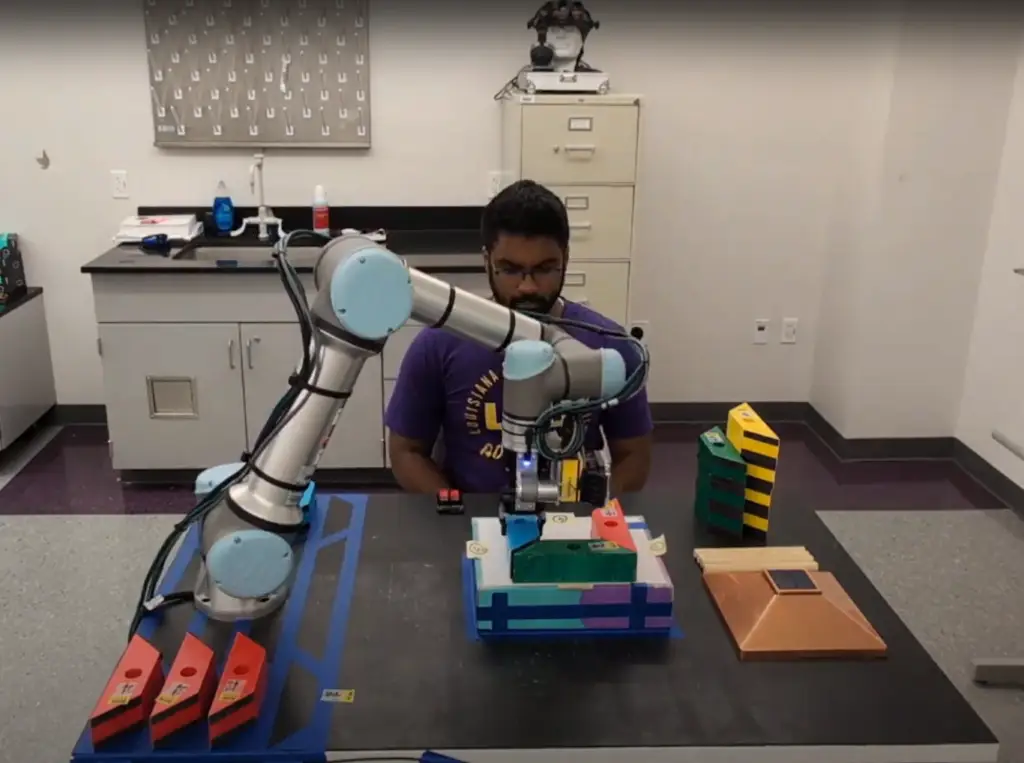
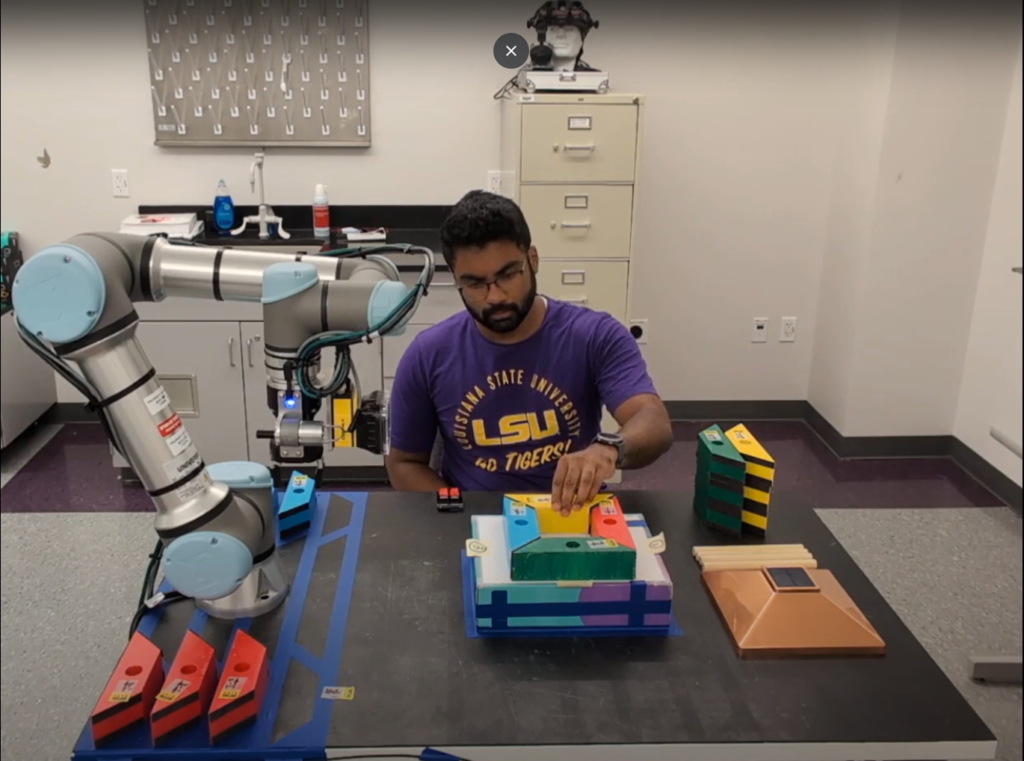
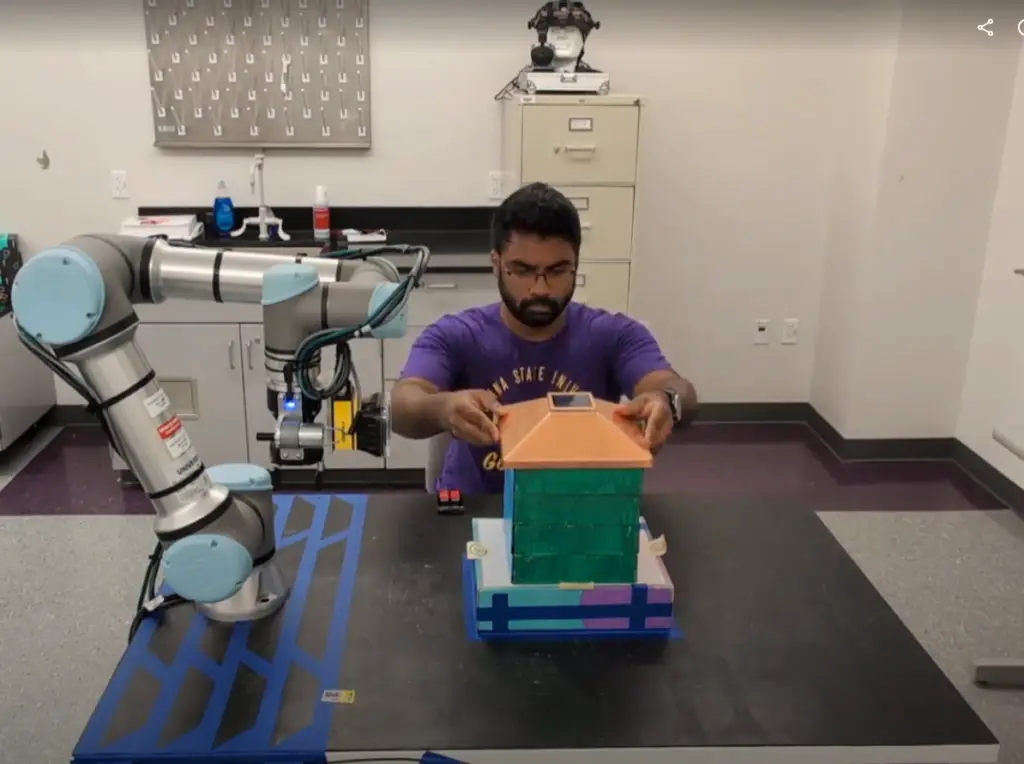
The participant and the robot collaborate to build an end product that resembles a miniature lamppost:
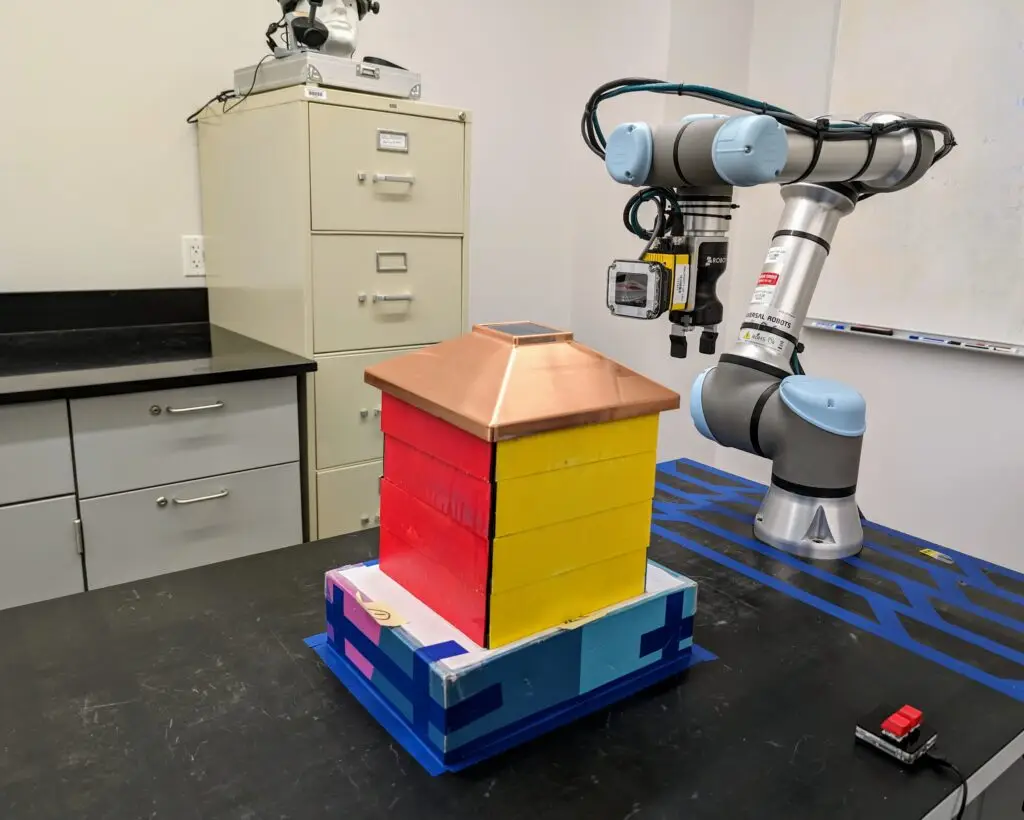
Outcome:
Task Performance:
– 22.3% faster completion time in the automated mode.
Mental Workload :
- No significant difference in HRV, HR, or NASA-TLX scores.
- Weak correlation in the automated mode: higher HR → slower DRT (possible cognitive overload).
- In the semi-automated mode: higher temporal demand → faster DRT (suggests engaged attention).
Trust in Automation:
- 4.6% higher trust scores in semi-automated mode.
- Significant increase in the Trust in Automation subscale for semi-automated group.
Key Correlations:
Automated mode: Higher workload = slower reaction times.
Semi-automated mode: More trust = slower, deliberate assembly; higher time pressure = quicker reaction.
Reflection:
While automation delivers measurable efficiency gains, users favored control and predictability in the semi-automated condition. This suggests that hybrid systems — where humans retain agency — can better maintain engagement and trust, even if they slightly reduce speed.
This work contributes to both HCI research and practical industrial cobot integration strategies, affirming that human-centered automation design is key for Industry 5.0.